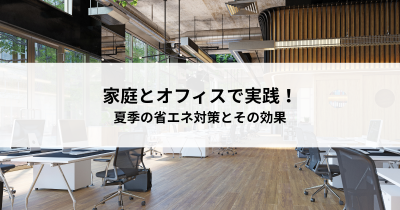
投稿日:2025.04.05
作業効率を上げる!製造業のための改善戦略
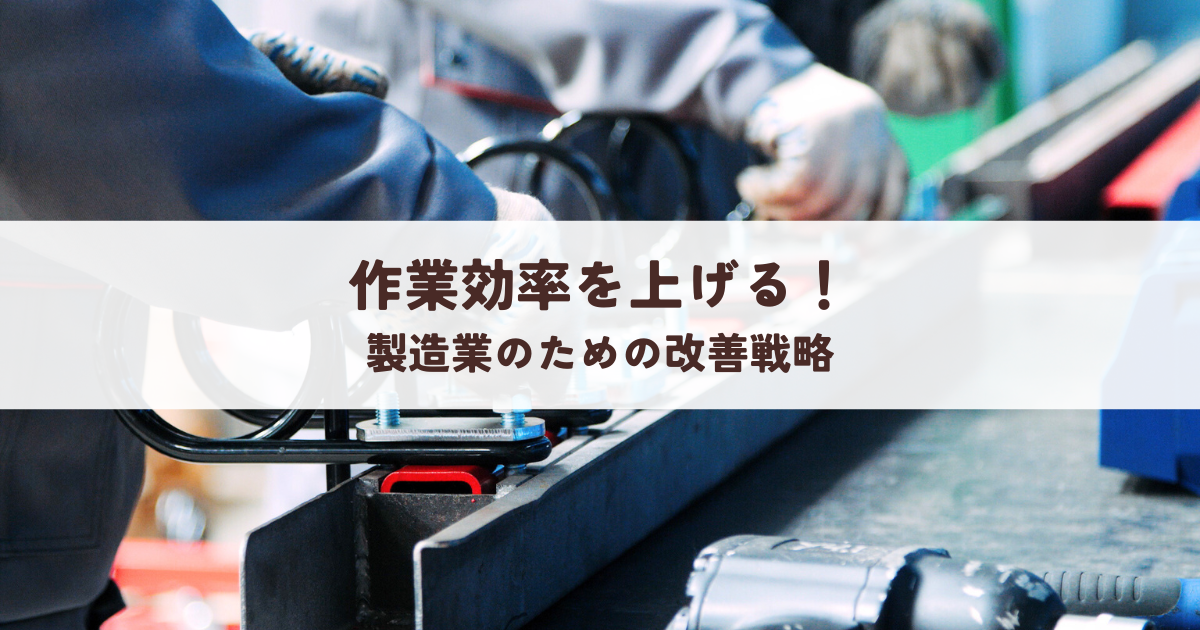
作業効率の悪化は、製造業にとって大きな課題です。
納期遅延やコスト増加、ひいては顧客満足度低下につながる可能性があります。
しかし、適切な戦略と対策によって、作業効率の向上は十分に可能です。
今回は、製造業における作業効率化のための戦略、その落とし穴と克服方法について解説します。
目次
製造業のための作業効率を上げる効率化戦略
作業効率低下の原因分析
製造業における作業効率の低下は、様々な要因が複雑に絡み合っています。
・人材不足:人材不足は、作業員の負担増加、疲労蓄積、ミス増加、ひいては全体の効率低下に繋がります。
熟練工の不足も、深刻な問題です。
・業務の標準化の遅れ:標準化されていない業務は、属人化し、作業のばらつきや品質の不安定さを招きます。
新人教育の遅れにも繋がります。
・在庫管理の問題:在庫不足は作業中断、余剰在庫は保管スペースやコストの無駄を発生させます。
いずれも効率低下に繋がります。
・他部門との連携ミス:部門間の情報伝達の遅れやミスは、再確認や修正作業といった無駄な時間を生み出します。
作業効率向上のための具体的な対策
作業効率の向上には、以下の対策が有効です。
・ムダ・ムリ・ムラの削減:5S(整理・整頓・清掃・清潔・躾)などの手法で、無駄な動作や時間を削減できます。
・業務プロセスの見直し:現状の業務プロセスを分析し、非効率な部分を洗い出し、改善することで、作業時間を短縮できます。
・マニュアルの整備:明確な作業手順を示すマニュアルを作成・整備することで、作業の標準化を促進し、ミスを減らせます。
・設備レイアウトの改善:作業者の動線を考慮した設備レイアウトにすることで、無駄な移動時間を削減できます。
作業効率化によるメリット
作業効率化は、生産性向上、コスト削減、品質向上、顧客満足度向上といった多大なメリットをもたらします。
生産量の増加による収益向上、人件費削減によるコスト削減効果も期待できます。
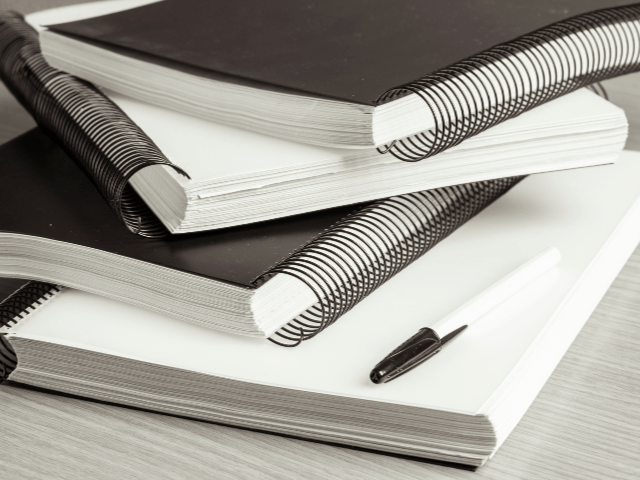
製造業における作業効率化の落とし穴と克服方法
よくある効率化の失敗例
効率化の取り組みが失敗に終わるケースとして、以下のようなものがあります。
・優先順位の未設定:全ての課題に同時に取り組むことは非現実的です。
優先順位を明確に設定し、段階的に取り組む必要があります。
・現場への負担増加:新しいシステムやツールの導入によって、かえって現場の負担が増加してしまうケースもあります。
導入前の教育やトレーニングが重要です。
・継続的な見直しの不足:一度改善策を導入したからといって、それで終わりではありません。
定期的に見直し、改善を継続することが重要です。
持続可能な効率化のための組織体制
持続可能な効率化のためには、組織全体で取り組む体制が必要です。
・トップダウンによる推進:経営層が効率化の重要性を理解し、推進することが不可欠です。
・現場の意見の反映:現場の意見を聞き入れ、改善策に反映させることで、より効果的な効率化を実現できます。
・継続的な教育・研修:従業員への継続的な教育・研修は、新たな技術やツールの習得を促し、効率化を支援します。
効率化と人材育成の両立
効率化と人材育成は両立させるべきです。
・効率化による余裕時間の活用:効率化によって生まれた時間を、人材育成に充てることができます。
・教育システムの整備:効率的な教育システムを整備することで、人材育成の効率化を図ることができます。
・モチベーション向上:効率化による成果を従業員に還元することで、モチベーション向上に繋がります。
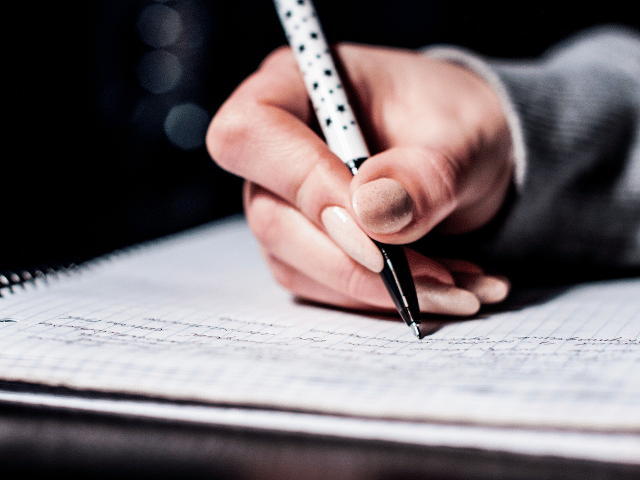
まとめ
製造業における作業効率化は、人材不足や競争激化といった課題への対応策として極めて重要です。
人材不足、業務の標準化の遅れ、在庫管理、部門間の連携といった課題を分析し、ムダ・ムリ・ムラの削減、業務プロセスの見直し、マニュアル整備、設備レイアウト改善といった対策を講じることで、生産性向上、コスト削減、品質向上、顧客満足度向上といったメリットが得られます。
しかし、効率化の取り組みは、優先順位の設定、現場への負担軽減、継続的な見直しといった点に注意を払い、組織全体で取り組む体制を構築することで、持続可能な成果を実現できます。
効率化と人材育成の両立も重要であり、効率化によって生まれた時間や資源を人材育成に充てることで、企業の持続的な成長に繋げることが可能です。