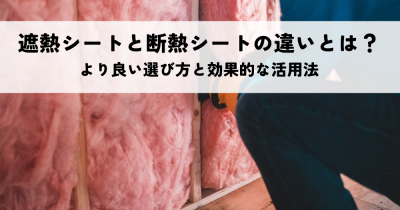
2025.07.11
工場の経営者や現場責任者の皆様、電気代や燃料費の高騰、CO2削減目標達成へのプレッシャーに悩んでいませんか。
近年、エネルギーコストの上昇や環境問題への意識の高まりから、工場における省エネ対策は喫緊の課題となっています。
本記事では、工場の省エネ改善事例をご紹介し、具体的な改善策を理解することで、自社の状況に合わせた省エネ対策を実行できるようにします。
目次
工場が省エネ改善に取り組む必要がある理由は、大きく2つあります。
近年、世界的なエネルギー需要の増加や原油価格の変動により、電気代や燃料費は高騰傾向にあります。
工場にとって、これらのエネルギーコストは大きな負担となっており、コスト削減の必要性が高まっています。
省エネ対策によってエネルギー消費量を抑制することで、電気代や燃料費の削減、ひいては工場全体の経費削減につながります。
地球温暖化対策として、CO2排出量の削減は世界的な課題となっています。
日本政府は2050年までに温室効果ガスの排出をゼロにする「カーボンニュートラル」を目指しており、企業も積極的にCO2削減に取り組むことが求められています。
工場は、製造プロセスや設備稼働によって多くのCO2を排出しているため、省エネ対策によるCO2排出量の削減は、企業の社会的責任を果たす上で重要な取り組みです。
具体的な省エネ改善事例をご紹介しましょう。
燃料炉の効率化は、工場のエネルギー使用を大幅に削減できる重要な改善ポイントです。
・炉壁の断熱材や塗料の改善
炉壁の断熱材や塗料を見直すことで、熱の損失を抑え、燃料消費量を削減できます。
最新の断熱材や遮熱塗料を採用することで、より効果的に省エネを実現できます。
・排ガスや排熱の再利用
燃料炉から排出される排ガスや排熱には、まだエネルギーが残っています。
排熱回収システムなどを導入することで、排ガスや排熱を有効活用し、他の設備のエネルギー源として再利用することで、省エネにつながります。
・バーナーの定期的な保守点検
バーナーの不完全燃焼は、燃料の無駄使いだけでなく、有害物質の排出にもつながります。
定期的な保守点検を行い、バーナーの燃焼効率を維持することで、省エネ効果を高められます。
ボイラーは、工場で蒸気を発生させる重要な設備です。
・蒸気圧力の設定見直し
ボイラーの運転状況に合わせて、蒸気圧力を適切に設定することで、エネルギー消費量を抑制できます。
必要な蒸気量に合わせて設定を見直すことで、無駄なエネルギー消費を抑えられます。
・スチームトラップの定期的な保守点検
スチームトラップは、ボイラーから発生した蒸気が凝縮した水を排出する装置です。
スチームトラップが故障すると、蒸気が無駄に排出されてしまい、エネルギー効率が悪化します。
定期的な保守点検を行い、スチームトラップが正常に動作していることを確認しましょう。
・ドレン排出の抑制
ボイラーから発生した蒸気は、配管内を循環する際に凝縮してドレンとなります。
ドレンを適切に排出しないと、ボイラーの効率が悪化し、エネルギー消費量が増加します。
ドレン排出量を抑制する装置などを導入することで、省エネ効果が期待できます。
工場では、電動機やポンプなど、多くの動力設備が使用されています。
・省エネベルトへの交換
電動機には、駆動用のVベルトが使われています。
このVベルトを省エネベルトに交換することで、摩擦抵抗を減らし、エネルギー消費量を抑制できます。
・インバータによる最適化
インバータは、電動機の回転数を制御する装置です。
インバータを採用することで、負荷に合わせて電動機の回転数を調整し、エネルギー消費量を最適化できます。
・無負荷運転の防止
電動機が負荷がかかっていない状態での運転は、無駄なエネルギー消費となります。
必要のないときは電動機の運転を停止したり、負荷に合わせて回転数を調整したりすることで、省エネ効果が期待できます。
工場の省エネ改善は、電気代や燃料費の削減、CO2排出量の削減など、多くのメリットがあります。
本記事でご紹介した省エネ改善事例を参考に、自社の状況に合わせた省エネ対策を検討し、実行することで、工場のエネルギー効率を向上できます。
省エネ改善は、企業の収益性向上だけでなく、地球環境保護にも貢献する重要な取り組みです。
屋根工事を検討している方は、100年以上続く信頼と実績のある屋根工事専門の会社である当社にぜひ一度ご相談ください。
2025.07.11
2025.06.11
2025.06.04
工場・倉庫の新たな暑さ対策
「スカイ工法」の施工なら
100年以上続く屋根工事会社、日本いぶしにお任せください。